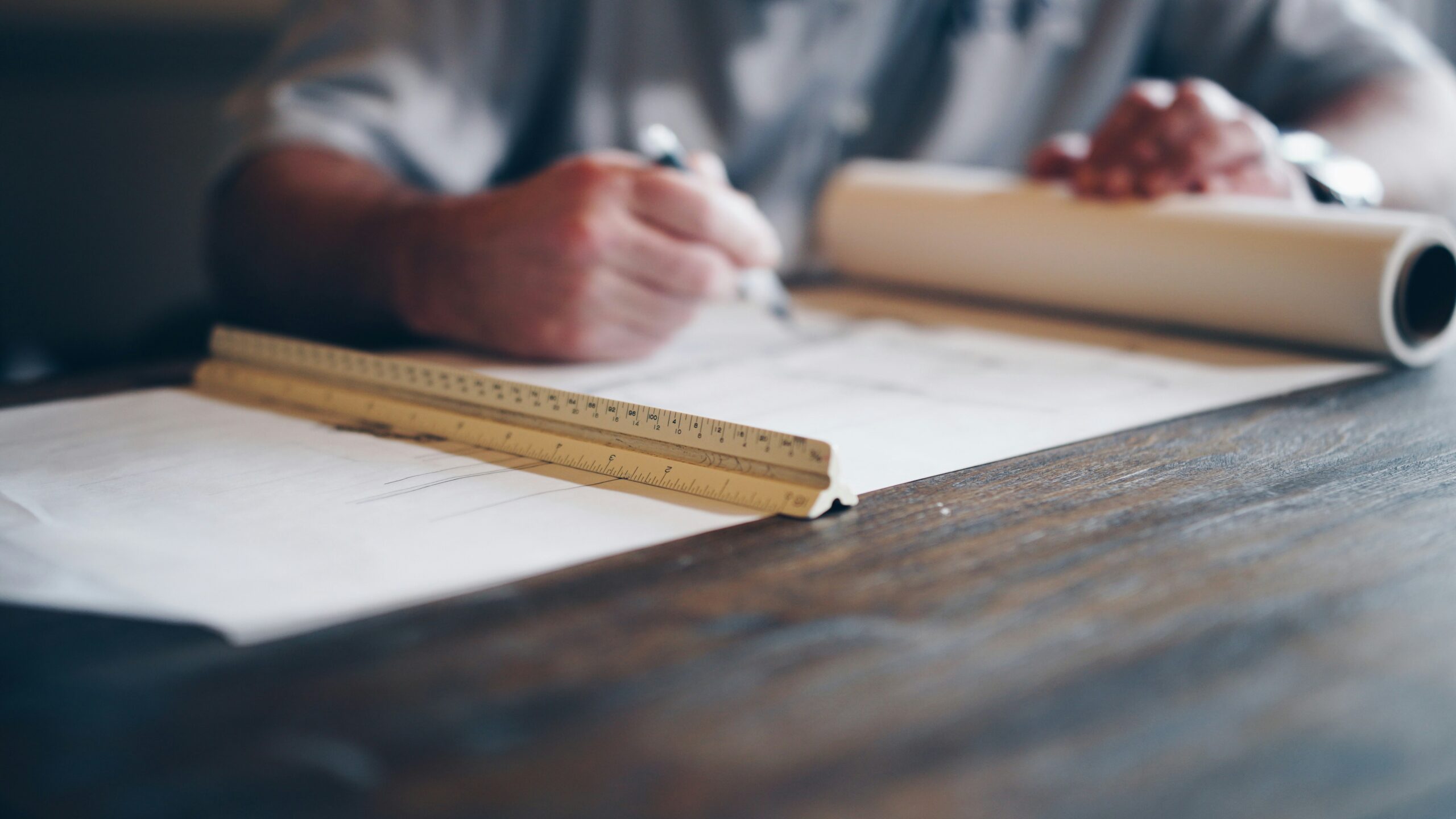
Cost vs. Quality: Finding the Right Balance in Construction
In the world of construction, balancing cost with quality is one of the most critical challenges faced by project managers and developers. Making informed decisions that do not compromise on safety, durability, or aesthetics requires a nuanced understanding of materials, processes, and market dynamics. Here’s how you can strike the right balance between cost and quality in your construction projects.
Understand Your Project’s Core Requirements
Before diving into any construction project, clearly define what you want to achieve. What are the non-negotiables in terms of structural integrity, safety, and functionality? Setting clear priorities helps in making decisions where quality cannot be compromised, allowing for flexibility elsewhere.
Choose the Right Materials
Selecting the right materials is crucial for maintaining quality. For instance, opting for higher-grade steel might be more expensive upfront but can significantly enhance the structural integrity of a building. On the other hand, for less critical components, more cost-effective materials might be sufficient without sacrificing the overall quality of the project.
Invest in Skilled Labor
Skilled labor is an integral component of any construction project. Experienced workers can often find more efficient ways to complete a task, potentially saving time and reducing material waste. Investing in skilled labor might increase initial costs but typically results in better craftsmanship and fewer errors, which can be more costly to rectify later.
Leverage Modern Technologies
Utilizing advanced construction technologies, such as Building Information Modeling (BIM) or prefabricated components, can help in reducing errors, speeding up the construction process, and cutting down costs while enhancing quality. These technologies allow for precise planning and adjustments before physical work begins, minimizing expensive changes during the build phase.
Long-term Thinking
Consider the lifecycle costs of your project, not just the initial expenses. Choosing cheaper materials and labor might save money upfront but can lead to higher maintenance and repair costs down the line. Quality construction with durable materials may come with a higher price tag but often leads to lower overall costs through reduced upkeep and longer lifespan.
Communicate and Collaborate
Effective communication among all stakeholders—architects, engineers, contractors, and clients—is vital. Being on the same page regarding the project’s budget, timelines, and quality expectations helps in aligning the team’s efforts towards balancing cost and quality effectively.
Regular Monitoring and Quality Control
Implementing strict quality control processes and regular monitoring throughout the construction phase ensures that the project adheres to set standards and specifications. This helps in catching and correcting errors early, potentially saving money and maintaining the desired level of quality.
Conclusion
Balancing cost and quality in construction doesn’t necessarily mean making compromises. By understanding your project’s essential requirements, investing in the right resources, and using modern technologies, you can achieve a balance that does not sacrifice quality for cost savings. A well-planned approach leads to successful project completion, ensuring durability, safety, and satisfaction for years to come.